Our journey began out of sheer curiosity about a new material and a desire to delve into different processes. Being situated in Canberra has afforded us the advantage of having the Canberra Glassworks nearby, enabling us to immerse ourselves in the local glass community and work intimately with many of its skilled makers. From these experiences, we've gathered valuable insights and are eager to share some of what we've learnt for those interested in venturing into glass design.
We've had the privilege of exploring glass design, culminating in the recent launch of our Haru and So lights in collaboration with Rakumba lighting.
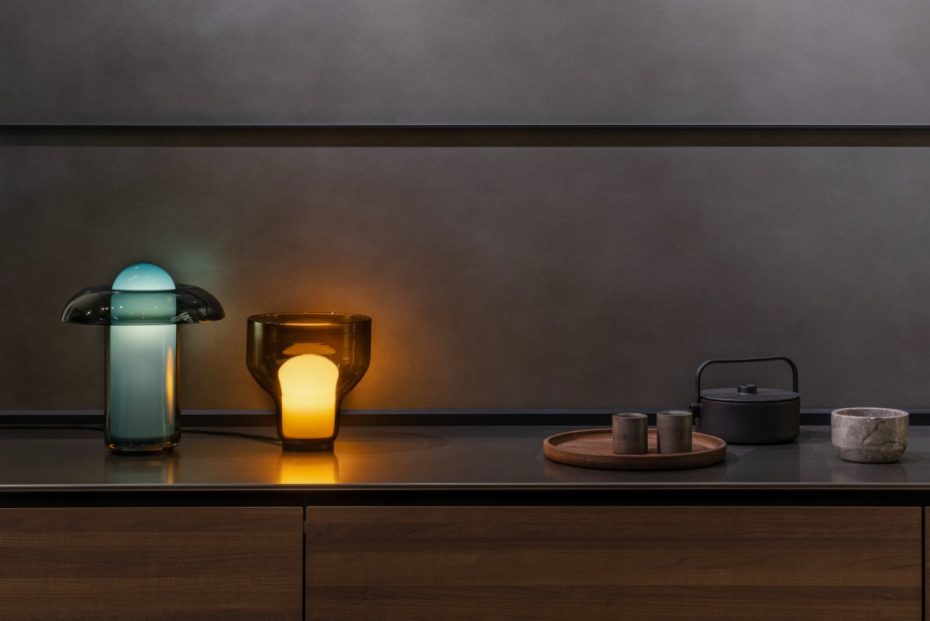
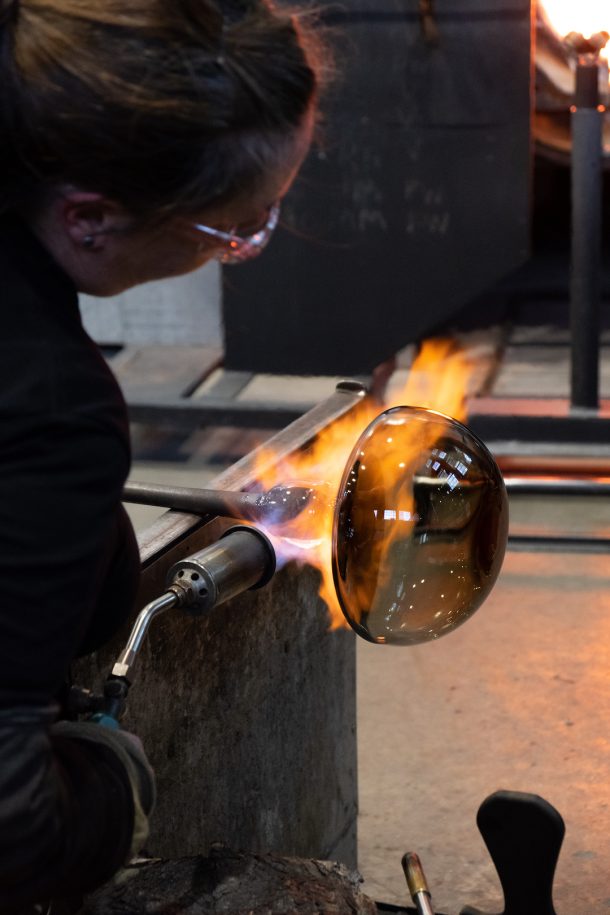
Get to Know Your Maker
This will allow you to understand the limitations of the material, or making process. By having these conversations early you can identify how difficult a piece will be to make, and possibly make changes to lower your manufacturing costs. It is also important to understand how your maker likes to work/communicate. Some will want detailed final drawings, others will want to be more involved throughout the process.
Designing for Repetition
If you’re designing a production piece you will want to make sure that the piece can be made quickly and easily. An efficient way to produce glass objects is to use a mould. Discuss this with your maker early on so you can design with this intention in mind.
Colour Selection
Consider how colour works in glass. There will be a difference in transparency, cost and saturation depending on what colour you choose. There will also most likely be a slight variance in the colour chosen and how it shows up in the final product.
Different Processes
Before designing a product get to know the possibilities in glass and the different processes on offer, this can guide your process. Some of the most common are; glass blowing, kiln forming and flameworking.
Cold working
All glass objects will be coldworked one way or another. There are various techniques that can be used to produce different finishes. Some are; polishing, Battuto (show here), engraving and beveling.
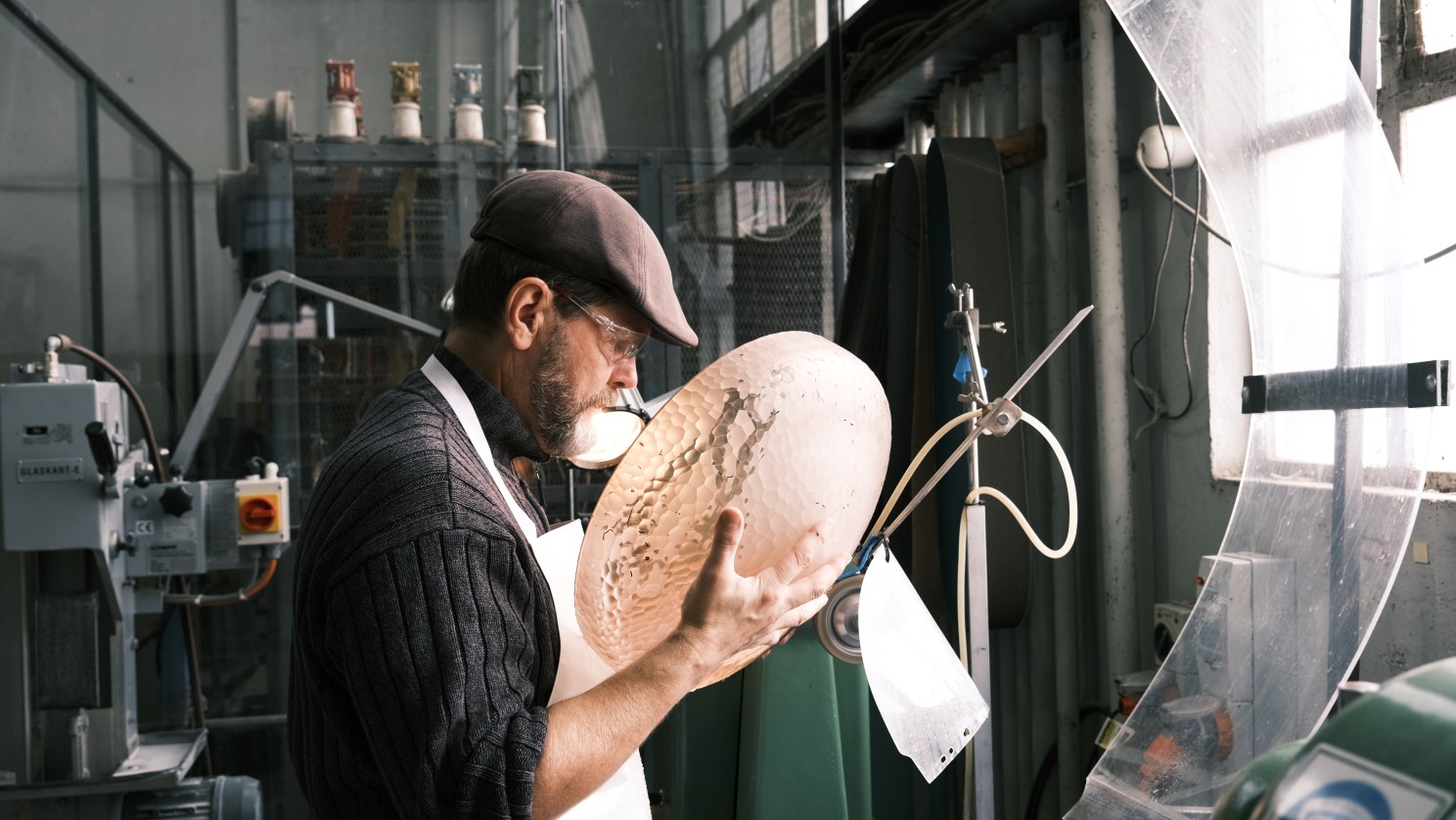